Cement backer board
The new kid under your tile
To say that the home building industry adapts to changes in technology a bit slowly would be a vast understatement. Professional builders have to warrant their work, and they are also concerned about their reputation. As a result, they adopt new techniques only when they are fairly certain that the change won’t end up as a call back.
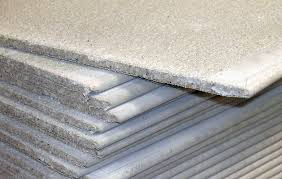
By building industry standards, Cement (backer) Board came onto the scene fairly recently. The first time I recall seeing it was in the mid 90’s when it appeared on the rack at one of our lumber yards. Cement board is a combination of concrete and reinforcing fibers formed into 3-foot by 5-foot sheets. These sheets are 1/4 to ½-inch thick and are typically used as a backing board for tile installations.
Cement board can be nailed or screwed across wood or steel studs. This creates a fast, really flat substrate for vertical floor tile or attached to plywood for stone or tile kitchen counters and backsplashes. It can also be used on the exterior of buildings as a base for exterior plaster (stucco) systems and sometimes as the finish system itself.
Cement board adds impact resistance and strength to the wall surface as compared to gypsum boards. Fabricating cement board in thin sheets allows bending for curved surfaces.
Thin set tile
Before cement board came along, many bathrooms in “tract” homes or spec-builds used a tiling method called “thin-set”. When it first got started, it was crap! Thin-set eliminated the traditional mortar layer beneath the tile. This saved time and material and required less skill. Thin-set was applied directly to a water-resistant version of gypsum sheetrock called “green” board because of its greenish color.
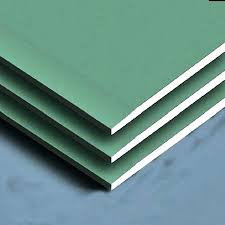
Unfortunately, “green” board did not resist impacts well nor did it stand up as a water-proof backing to the tile. Tile cracks, caulking or mortar failure could lead to water damage and sometimes mold.
Backer board makes Thin-Set tile acceptable
As a tile backing product, Cement Board has far better long-term performance than paper-faced gypsum core products. It is concrete after all, not gypsum. As a result, it will not mildew or physically break down in the continued presence of moisture or leaks. Also, cement board provides a stronger bond and support with tiles than typical gypsum board. Cement Board has made thin-set tiling an acceptable building practice.
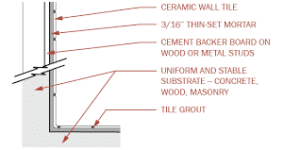
Tough but not waterproof
Cement board resists water damage but is itself not waterproof. It will actually absorb moisture, but it has excellent drying properties. In areas continually exposed to water like spray from showers, a waterproofing material is required behind the sheets, Plastic waterproofing sheets can be used or perhaps a trowel-applied liquid membrane.
Weight and installation
One major disadvantage of cement board is the weight per square foot. It is approximately twice that of gypsum board, making handling by one person difficult. Cutting of cement board must also be done with carbide-tipped tools and saw blades. Due to its hardness, and brittleness, pre-drilling for fasteners is recommended. Cement board is hung with corrosion resistant screws or ring-shank nails.
Cement board has very little movement under thermal stress. Still the boards are usually installed with a slight gap at joints in shower pans, bathtubs, and each other. These joints are then filled with silicone sealant or the manufacturer’s taping compounds before applying a finish. Joints are taped like conventional gypsum board, but with fiberglass tapes that provide additional water resistance.
Summary
Combined with a water impermeable finish, cement board is a stable, durable backing board. Cement board is slightly more expensive than water-resistant gypsum board but will certainly provide better long term value.